Forklift Accident Prevention: Understanding Risks and Enhancing Safety
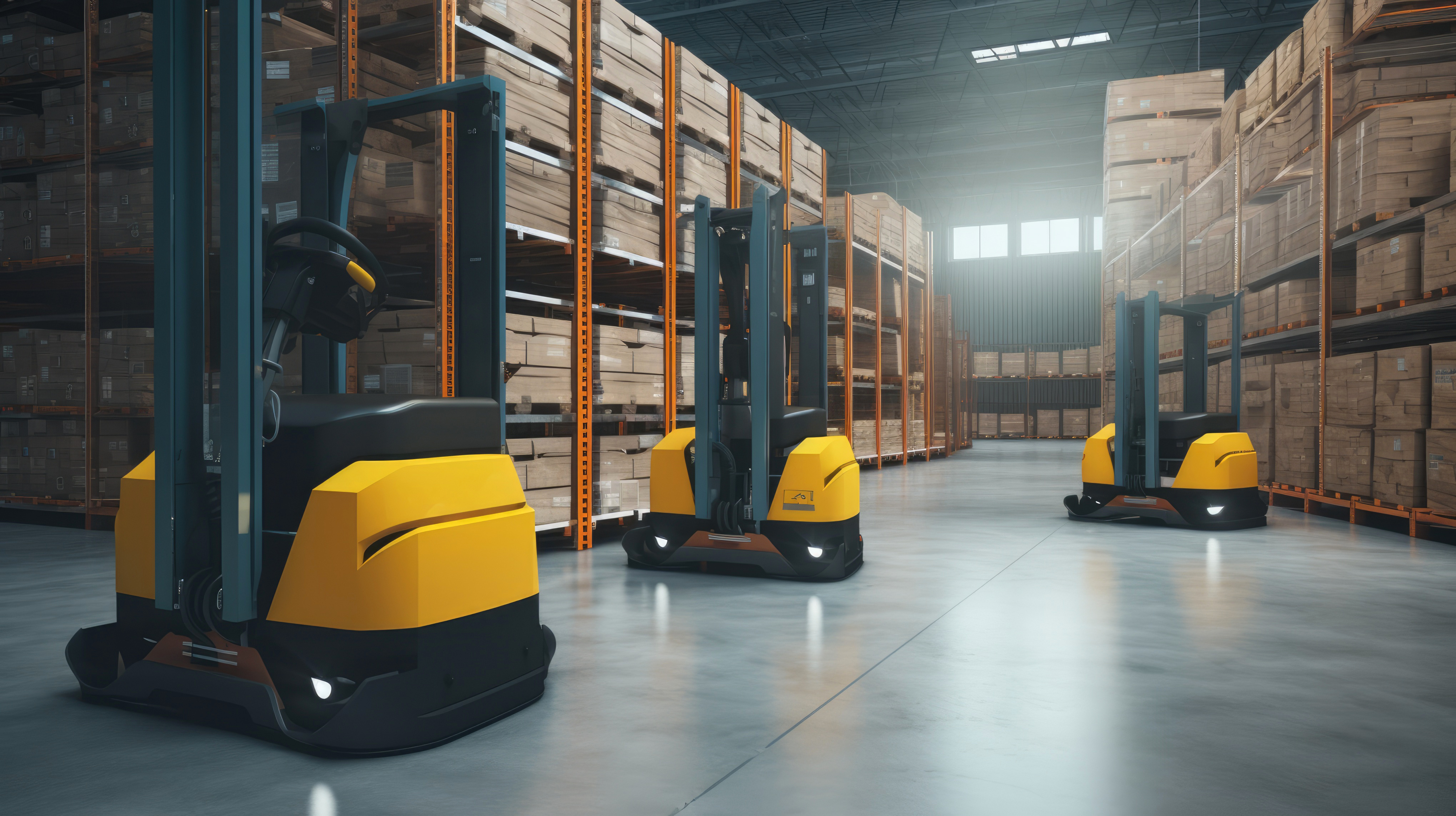
Forklifts are a common fixture on many work sites, and are essential to daily logistics operations and moving goods through the supply chain. However, forklifts are also a common cause of workplace accidents, with an estimated 90,000 forklift-related safety incidents each year.
Let’s examine the risks associated with forklift operations and look at ways to use safety protocols and smart technology to enhance workplace safety and prevent forklift accidents.
Forklift Accidents: The Alarming Statistics
Forklift accidents pose a significant risk in various industries, and they are more common than you may realize.
According to the National Safety Council (NSC), Forklift accidents caused 70 work-related deaths in 2021 and 7,290 nonfatal injuries involving days away from work in 2020.
The average cost to a business for a workplace injury, including medical and administrative expenses, and productivity losses, is an estimated $42,000 per incident, with the cost of serious and fatal injuries much higher. That means that, in addition to the human loss, forklift accidents also have a severe financial implication.
An estimated 25% of forklift accidents are due to improper or inadequate operator training, suggesting that enhancing training protocols could make a big impact on forklift safety.
Common Forklift Accidents: Causes and Consequences
Understanding the causes behind forklift accidents can help identify areas for improvement. In addition to insufficient training, some common causes of forklift accidents include:
- Negligent operation: Speeding, reckless driving, and improper load handling are significant contributors to forklift accidents, which is oftentimes a product of improper training and certification.
-
Inadequate maintenance: Neglecting regular inspections and maintenance can result in malfunctioning equipment and increased accident risks.
-
Poor worksite design: Congested work areas, inadequate signage, and a lack of designated pathways can make forklift navigation difficult, ultimately leading to accidents.
These circumstances can lead to forklifts colliding with objects, tipping over, or striking pedestrians. The consequences can be physical, financial, and psychological and could leave operators and other staff with severe injuries, including fractures, crush injuries, and even fatalities. Not to mention property damage to infrastructure, equipment, and inventory, legal liabilities, medical expenses, and increased insurance costs– as well as reduced employee morale and decreased productivity as a direct result of the lack of safety and trust on the worksite.
Preventing Forklift Accidents
Many forklift accidents are preventable with the right safety protocols in place. Compliance with OSHA regulations and guidelines for forklift safety, including proper operator training, equipment maintenance, and safe work practices, are essential to improve worksite safety.
In 2014, the Industrial Truck Association started National Forklift Safety Day to raise awareness of the safety issues related to forklift design and operation. Many forklift manufacturers and operators use this day as an opportunity for conversations about crucial safety protocols and accident prevention.
Some examples of effective strategies for improving forklift safety include:
- Comprehensive operator training and certification programs.
- Ensuring that only authorized, approved personnel have access to operate forklifts.
- Implementing safety checklists and equipment inspections prior to forklift use.
- Using smart machine technology to collect and analyze data on safety incidents.
- Promoting a culture of safety through regular safety meetings, reporting near misses, and rewarding safe behaviors.
Autonomous Forklifts for Worker Safety
The advent of autonomous and remote-controlled forklifts offers another opportunity to enhance worker safety.
Autonomous or remote-controlled forklifts allow personnel to keep a safe distance from machines while they are in motion. AI can be used to avoid collisions and implement restrictions on vehicle speed. These forklifts can also reduce operator fatigue and allow personnel to focus on more essential, less repetitive tasks in the workplace.
However, autonomous forklifts come with their own risks, requiring safety technology and specific protocols to ensure their safe operation.
Safe wireless control is essential for these systems. Even the smartest machines can make mistakes or encounter unexpected situations.
If a sensor fails, a machine gets stuck, or a site-wide safety incident occurs, workers need to be able to intervene immediately via reliable wireless communication. Global E-Stop, or a system that allows all machines to be commanded at once, is important for ensuring safety.
Cybersecurity is also important for autonomous forklifts. Since they rely on connected technology, security measures must be implemented to protect them from potential internet-based threats.
Enhancing Forklift Safety
Forklift accidents are a significant concern in workplaces, leading to injuries, property damage, and financial losses. By understanding the risks associated with forklift operations and implementing proper safety protocols, organizations can significantly reduce the occurrence of accidents.
To future-proof work sites and mitigate risks, autonomous forklifts offer an innovative approach to further improve worker safety. By integrating advanced technology and robust protocols, we can strive for accident-free workplaces and ensure the well-being of employees, because prioritizing safety today leads to a more secure and productive tomorrow.
At FORT, we help users and builders of forklifts and other automated systems to accelerate development, maximize productivity, and keep valuable assets and people safe. Our trusted wireless control technology can add global e-stop capabilities to autonomous forklifts, give operators the ability to take temporary control of autonomous systems, and help ensure that machines and data are protected from cyberattacks.
For more information on how FORT can help you maximize uptime and keep your forklifts or other machines safe, schedule a meeting with one of our experts.